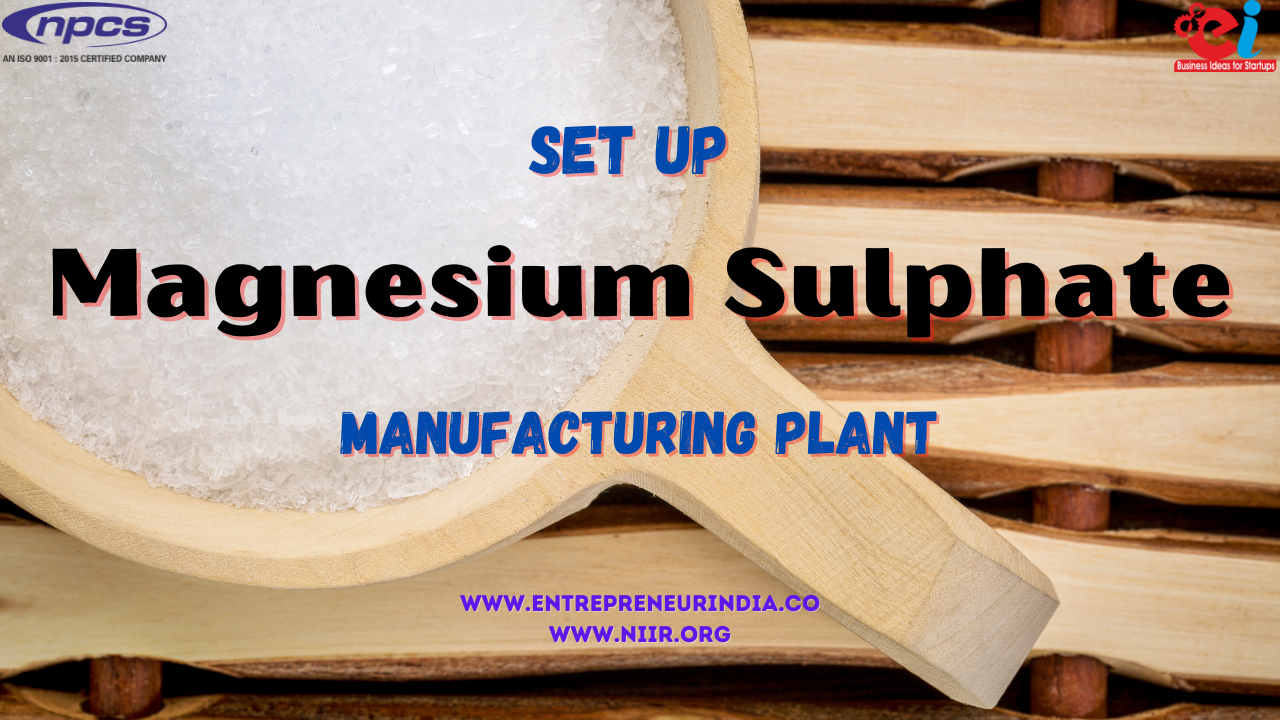
Setting up a magnesium sulphate manufacturing plant can be a highly profitable industrial venture due to the widespread use of magnesium sulphate across agriculture, pharmaceuticals, textiles, chemicals, and food processing. Commonly known as Epsom salt, magnesium sulphate is an inorganic salt with a wide range of industrial and commercial applications. It is used to improve soil fertility, as a drying agent in chemical reactions, in medicine as a saline laxative, and in animal feed supplements. With an increasing demand for fertilizers and a shift toward micronutrient-rich farming practices, the market for magnesium sulphate is growing steadily, especially in agriculture-driven economies like India. Entrepreneurs with access to raw materials, basic chemical processing knowledge, and compliance resources can generate significant returns by establishing a magnesium sulphate manufacturing plant.
Market Demand and Business Opportunity
The demand for magnesium sulphate has seen significant growth over the years, driven by the agriculture sector where it is used as a magnesium and sulfur nutrient. Magnesium deficiency in soil is a common problem, especially in regions with intensive farming. This has led to an increase in demand for magnesium sulphate as a soil amendment. In addition to its agricultural use, magnesium sulphate is used in pharmaceutical preparations, as a stabilizer in textiles, in detergents, and even in personal care products. Setting up a magnesium sulphate manufacturing plant enables entry into multiple industrial segments with steady and scalable demand. As the product is cost-effective, non-toxic, and environmentally safe, it continues to gain acceptance, especially in organic and sustainable farming models.
Visit this Page for More Information: Chemical Industry Projects
Types and Grades of Magnesium Sulphate
Magnesium sulphate is manufactured in different grades depending on its end use. The most common form is magnesium sulphate heptahydrate (MgSO?·7H?O). There are also monohydrate and anhydrous grades, each used for specific industrial applications. Agricultural-grade magnesium sulphate is typically produced in granular or crystalline form and packaged in bulk for farms. Pharmaceutical-grade variants require higher purity standards and are used in intravenous or oral drug formulations. Your magnesium sulphate manufacturing plant must decide on the grade based on the targeted market segment—bulk fertilizers, pharma, feed additives, or industrial usage. Each grade has distinct purity requirements and processing standards, which influence production setup, quality control, and pricing.
Related Project Report: Profitable Business of Magnesium Sulphate
Raw Materials and Chemical Process
The major raw materials required for a magnesium sulphate manufacturing plant include magnesium oxide (MgO) or magnesium carbonate (MgCO?) and sulfuric acid (H?SO?). The chemical reaction between these ingredients produces magnesium sulphate along with water and carbon dioxide (in some reactions). The overall process is straightforward and involves a reaction tank, filtration, crystallization, and drying stages. The final product is then packed in bags or containers depending on customer needs. Proper reaction control, impurity removal, and moisture control are important to achieve a high-quality, market-acceptable product. In some advanced units, additional purification steps are included to meet pharmaceutical or food-grade specifications.
Read Similar Articles: Chemical Industry
Plant Setup and Infrastructure
Setting up a magnesium sulphate manufacturing plant requires adequate land, preferably in an industrial zone with access to utilities like water, power, and road connectivity. The infrastructure includes raw material storage tanks, reaction vessels (mild steel or SS-lined), filtration units, crystallizers, drying equipment (tray dryers or rotary dryers), and packaging machinery. For small-scale production (5–10 tons/day), an area of 3,000–5,000 sq ft is sufficient. Larger units with 25+ TPD capacity need proportionately more space. The plant should also include lab facilities for quality testing, a wastewater handling system, and safety gear for handling acid and chemical reactions.
Related Feasibility Study Reports: Chemicals (Organic, Inorganic, Industrial) Projects
Machinery and Equipment
The key machinery needed for a magnesium sulphate manufacturing plant includes reactors, agitators, acid dosing systems, heat exchangers, filtration units, centrifuges, crystal formers, dryers, and packaging lines. The selection of machines depends on production volume, type of product (flakes, crystals, powder), and required purity level. Semi-automatic plants are sufficient for moderate production volumes and cost-effective for startups. Advanced fully automatic lines with continuous crystallization and drying are prefere for large-scale and export-oriented units. Always ensure that machinery is corrosion-resistant and capable of handling acidic environments.
Read our Books Here: Chemical Technology (Organic, Inorganic, and Industrial), Fine Chemicals
Licensing and Regulatory Requirements
Manufacturing magnesium sulphate requires several regulatory approvals, especially if the product is to be used in food, pharma, or agriculture. A magnesium sulphate manufacturing plant must obtain factory registration, pollution control board clearance, hazardous material handling licenses (for sulfuric acid), GST registration, and trade licenses. If manufacturing food or pharma grade, additional FSSAI or drug department approvals may be require. Certification from agencies like ISO or BIS helps in gaining customer trust and eligibility for government tenders or export markets. Safety norms for chemical handling and material storage must be strictly follow to avoid penalties and ensure employee well-being.
Workforce and Human Resource Needs
The plant needs a trained workforce to handle operations, quality control, maintenance, and administration. For a basic magnesium sulphate manufacturing plant, a team of 8–15 people is adequate including chemical engineers, machine operators, lab analysts, and packaging staff. As the plant scales, the workforce can be expand with dedicat roles for safety officers, logistics managers, and export coordinators. Basic training in chemical handling, process monitoring, and first aid is essential. Retaining skilled personnel ensures consistent production, safety, and quality.
Cost of Investment and ROI
The cost of setting up a magnesium sulphate manufacturing plant depends on the capacity, automation level, and plant design. A small unit with 5–10 TPD capacity may cost around ?30–50 lakh, including machinery, land development, civil work, and licenses. A medium-sized plant with 25–50 TPD can cost ?1–2 crore. The operating cost includes raw materials, labor, utilities, maintenance, and packaging. The gross profit margins are attractive due to relatively low input costs and stable product pricing. With proper market linkage, your plant can achieve break-even within 1.5 to 2 years. Government subsidies under MSME and agro-processing schemes can further reduce the financial burden and improve ROI.
Packaging, Branding, and Distribution
Depending on your market, magnesium sulphate can be sold in 25 kg, 50 kg, or bulk jumbo bags. Proper moisture-proof, labeled packaging is essential to ensure quality during transport and storage. If targeting retail, consider branded packaging with certifications, usage instructions, and batch numbers. Your magnesium sulphate manufacturing plant should develop a distributor network across agricultural zones, agro-input retailers, pharma ingredient traders, and industrial buyers. Participating in agricultural expos, partnering with cooperatives, or listing on B2B platforms can enhance visibility and sales.
Sustainability and Waste Management
The manufacturing process, while simple, generates some acidic effluents and waste. Your magnesium sulphate manufacturing plant should include an effluent treatment plant (ETP) to neutralize and recycle water. Using scrubbers for sulfur fumes, and ensuring safe storage of sulfuric acid, are critical for environmental safety. Sustainable practices like heat recovery systems, solar panels, and green belts can also enhance your plant’s compliance and CSR image. Proper documentation of waste handling and EPR norms is necessary, especially for ISO certification or export units.
Final Thoughts
Launching a magnesium sulphate manufacturing plant offers an attractive opportunity to serve multiple industries with a single, high-demand product. From agriculture and pharma to industrial chemicals and textiles, magnesium sulphate plays a vital role in improving product quality and performance. With moderate investment, easy raw material availability, and straightforward production, this business is ideal for MSMEs and chemical entrepreneurs. A well-planned setup with a focus on quality, regulatory compliance, and market reach can establish your plant as a reliable player in the chemical manufacturing space. With rising global demand for micronutrients and sustainable fertilizers, now is the right time to invest in this growing sector.
Watch other Informative Videos: Chemicals (Organic, Inorganic, Industrial)
See More Links:
- Start a Business in Asia
- Start a Business in Potential Countries for Doing Business
- Best Industry for Doing Business
- Business Ideas with Low, Medium & High Investment
- Looking for Most Demandable Business Ideas for Startups
- Start a Business in Africa
- Start a Business in India
- Start a Business in Middle East
- Related Videos
- Related Books
- Related Projects
- Related Market Research Reports
NIIR PROJECT CONSULTANCY SERVICES, DELHI
An ISO 9001:2015 Company
ENTREPRENEUR INDIA
106-E, Kamla Nagar, Opp. Mall ST,
New Delhi-110007, India.
Email: npcs.ei@gmail.com
Tel: +91-11-23843955, 23845654, 23845886
Mobile: +91-9097075054, 8800733955
Website: https://www.entrepreneurindia.co
https://www.niir.org